Tension is due to forces pulling against each other and when applied to processes involving moving webs, it is necessary for the sake of production efficiency, that these opposing forces are stabilized at a set value which is applicable to both the material and the process.
Tension is an invisible force, so unless the correct regulating equipment is in place the result of incorrect tension may not become apparent until, in the case of some converted products, it is delivered to the end user. This is particularly so in the case of stretch films and laminates.
The correct tension, regardless of material, is dependent not only on its modulus of elasticity but also on the process which is being carried out at the time. To cite one example, a flexographic printing press engaged in printing on thin gauge plastic film will require a different set of tension values for the unwinding process, a different set of tension values for the printing process, and for slitting, and for rewinding.
Unit tension, or force per unit width, is arrived at by consideration of the thickness and the type of material. Units are typically measured as pounds per linear inch (PLI), as newtons per centimeter (N/cm) or as kilograms per centimeter (Kg/cm). The paper industry favors the method whereby tension is quoted in terms of the unit paper weight (lbs/3,000 sq.ft., grams/square meter). There are several sources available for guidance in determining reference tension values for a particular material in a particular process.
Maintenance of correct web tension is essential at every stage of the process. In the case of converting machines, most will have at least two separate tension zones and sometimes as many as ten. When unwinding a roll of material, the tension needs to be set at a constant value, high enough to allow the web to pass over rollers without slippage and without causing wrinkles, but not so high as to cause stretching and web breaks.
When engaged in coating applications, it is important that the coating is laid down consistently and evenly. In this situation the tension gradient across the web is as critical as the total web tension in the machine direction for obtaining a uniform and repeatable coating weight.
Constant tension control is of prime importance in the printing of multiple color work in register, where the web is held only by tension. Minor variations in tension of the web between color stations will result in out-of-register print and unusable product. In the case of laminating two or more webs together, the relative tension between the two webs is critical to avoid sheet curl or delamination of the finished product. Accurate tension control is also needed on rewinders to make the perfectly formed reels for transportation and further processing.
As you can tell from the above examples, tension control is a critical factor of production. For maximum production efficiency, reduced waste and minimum down time, tension control can not and should not be left to chance. There are three primary methods on the market which have been devised to control and manage tension. These are: manual control method (100% operator-dependent), open-loop systems, which work with no direct feedback from the actual web and partial operator involvement, and closed-loop systems utilizing dancer rolls or load cells (transducers) for direct web feedback and minimal operator involvement.
The manual method is quite operator-intensive and requires that the operator continually adjust the torque as the roll diameter changes. This method is the least precise, and only slightly better than not doing anything at all (figure 1), and may only be appropriate if the tension tolerance is quite large (figure 2).
The open-loop method provides a more automated and accurate adjustment of torque as the diameter changes, resulting in much smaller tension errors than the manual method. This method relies on the fact that in the case of an unwinding roll or a rewinding roll, the tension is directly proportional to the torque at the winding shaft divided by the roll radius. If the torque is not changed as the diameter decreases, tension will rise.
By continuous monitoring of roll diameter, the brake or drive responds to the given signal and adjusts accordingly. The monitoring of the diameter can be done by using some sort of mechanical (rider) arm, by electronic calculation or through the use of ultrasonic or laser sensing devices. The open-loop method can only control the brake in relation to diameter and is suitable for machines handling strong and inexpensive materials or in situations where the tension tolerance is greater than 5% of web tension. The accuracy of the system is also is extremely dependent on the brake or drive exhibiting linear torque characteristics.
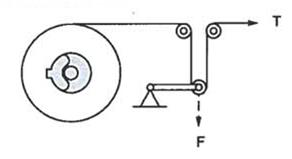
The dancer roll system of closed-loop tension control is an effective method in that it controls web tension by using a moving roller or assembly. Although classified as a tension control system, in reality it is more of a variable speed detector with the tension produced as an effect of the force loading of the dancer roller on the web.
Dancer systems operate by balancing web tension force with the force loading of the roller, usually applied by air cylinders. The control system keeps the dancer position constant by adjusting input or output of web speeds. This moving roller assembly provides storage in the web that can provide useful benefits in a web production line. This is especially helpful in applications utilizing flying splice, indexing, as in bag formation or to address rapid acceleration and/or deceleration of the production line.
The pneumatically loaded dancer arm generally produces output pressure in direct relation to the position of the arm. A dancer controller regulates the brake so that the position of the arm will not alter as the reel changes diameter.
One drawback to this system is that it tends to be more mechanically complex than the other systems, and therefore accurate results can only be consistently achieved when the control system is well maintained. After a time, operational characteristics can change and instability can occur, leading to production problems. Dancer systems also require more valuable machine space to install, which often makes retrofits impractical. Another drawback is the fact while they can be effective tension control systems, they cannot measure or display the actual web tension. The web tension is determined by the load applied to the dancer arm air cylinders, and therefore do not provide any direct measurement or indication of the actual web tension. The tension can be calculated, and inferred by the relative load on the dancer arm, but it is not a direct measure.
The most accurate way to control any variable on the web is to measure it, then compare it with the required value and for electronic mathematical compensation to occur. This is the function of the closed-loop load cell (transducer)-based tension control system.
The only way of continuously measuring the tension in a moving web is for the web to pass over a roller fitted with load cells (or transducers) that can measure the force on that roller caused by the combination of tension and the angle of wrap around that roller. The resulting signal can be used simply as a measure of the tension but is nearly always compared with a signal representing desired web tension or set point. The error between the two is then processed by a control amplifier to provide stability in the web.
The control output is amplified and converted either to air pressure to work a pneumatically actuated brake, an electric signal for an electric or magnetic particle brake or to a motor controller. As the diameter of the roll changes at either the unwind or the rewind end of the machine, the closed-loop control will automatically adjust the brake or drive to compensate for the changing diameter and mass of the roll to maintain the desired tension levels for consistent, quality production. Because the process is measured, and monitored, it can be easily repeated for different substrates and different process to provide consistency to the process, reduce waste, and improve quality, resulting in maximum productivity.
When determining which method of control is appropriate for the given application, several factors require careful consideration. What are the characteristics of the substrates to be processed? What does the process itself demand of the substrate? What is my tension tolerance? What is the value of the web and what impact does scrap rates have on the bottom line? Each approach to tension control has specific costs associated with them. The solution you choose can be determined by simple payback analysis or in overall impact on runability and productivity. In any case, a proper tension control strategy cannot be overlooked.
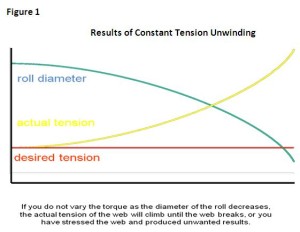
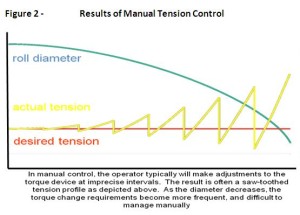
© Montalvo – Permission granted to use this copyrighted material, in part or all, provided that the source is acknowledged as © www.montalvo.com