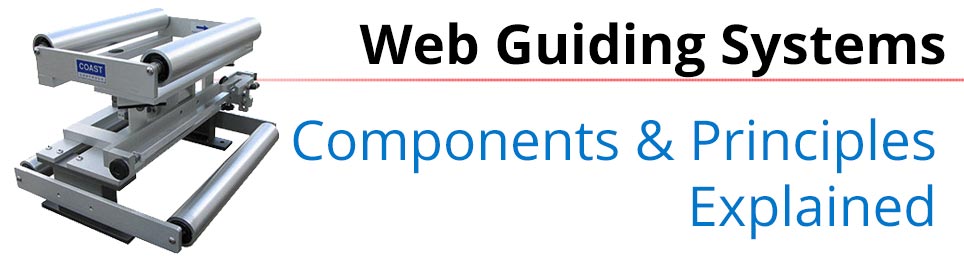
Web guiding systems are necessary to properly align web material being transported through roll-to-roll converting machines. Without web guiding systems and principles a number of factors such as process variations in tension and speed, material property variations in regard to quality, improperly maintained machines, changes in traction and so on, can affect the proper alignment of material. The following are several the general principles and concepts behind web guiding systems:
How Does a Web Guide Work?
Web guides work to keep material aligned while being transported through a web. When moving through rollers, web materials tend to align themselves perpendicular to the axis of the rollers. Without a guiding system in place the material would misalign (think of how easily a garden hose telescopes when rolling it up on a retractable reel).
As any flexible material is transported through a web it is subjected to the “normal entry rule” – which basically means that the rollers in the converting machine must be aligned properly. Normal entry must be applied when transporting webs or the results will be much like the garden hose – misaligned. Normal entry is accomplished by deliberately setting or programming the axis of rotation of the guide roller in order for the material to be steered or guided into a different position.
Web Guide Components
The basic components of a typical web guiding system consist of a guide mechanism, an actuator, a position or web edge sensor, and a controller. A web guide mechanism is the mechanical device that makes contact and moves the web material. The mechanism comes in various shapes and sizes depending on the machine. Web guide mechanisms are guided along by an actuator, which moves the web to the correct location.
As the name suggests, a web edge sensor detects the position of the web as it travels through the web guide mechanism and the sensor’s position is the reference point that the web will be guiding to.
Controllers are used to manage the web guiding system. The controller uses readings from the sensors to take necessary corrective measures and actions. Once processed, the controller sends a corrective command to the actuator to adjust the guide mechanism to actively control the web position.
Web Guide Types
Essentially, there are two types of web guides utilized in the industry. Displacement guides, also referred to as offset-pivot guides, and steering guides or remotely pivoted guides. Displacement guides are the more commonly used of the two. The simple design uses a two roller system that rotates around an “imaginary” offset-pivot point (hence the name). Properly installed displacements guides greatly reduce the stresses on a web. Displacement guides can utilize existing idler rolls for the “lead-in & exit” rollers or can be provided with additional rollers for proper functionality & performance following general geometric principles. Due to this they can fit into tight spaces and orientated however needed.
In contrast, steering guides correct by moving the web laterally while simultaneously pivoting the web in the same direction. This offsets the web’s inclination to return to its prior position. The guide (single or double roller) must be installed after a long, free-entering span to avoid wrinkling while following general geometric principles for proper functionality & performance.
Unwind Web Guides
Commonly called “shifting stands”, unwind guides are a kind of terminal web guide that require no pivoting motion when aligning the web material into a converting machine. Unlike the terminal web guides, no pivoting motion is necessary for these types of web guides. Unwind guiding is obtained by automatically positioning an unwinding roll of material mounted on a laterally shifting roll stand carriage. A shifting idler roller is attached to the stand. The sensor is fixed and mounted independent of the stand.
Rewind Web Guides
Commonly called “shifting rewinds”, are located at the end of roll-to-roll machines, and are one of the tools used to ensure that the wound roll is not telescoping. Rewind guiding commonly referred to “chasing” provides edge position controls by having the shifting stand and attached sensor ‘chase’ any web misalignment as the roll is winding to align each new wrap or layer of the wound roll. A fixed idler roller is required between the sensor and the rewinding roll.
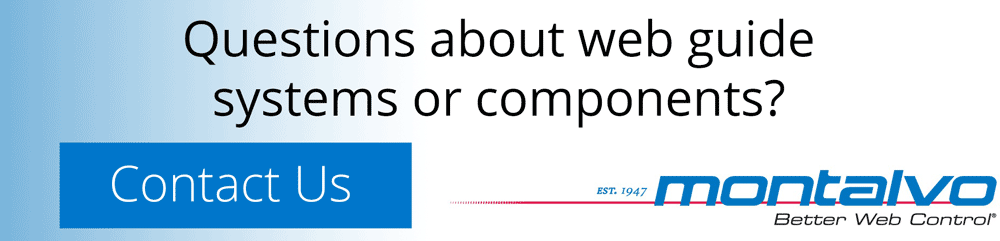