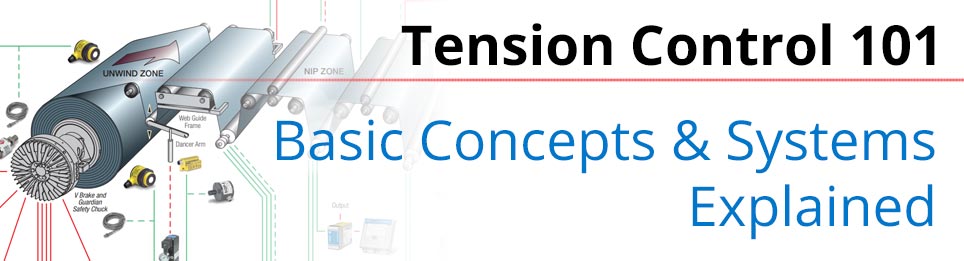
What is Tension?
Tension is the pull or strain put on a web of material that tends to stretch it in the machine direction. It can be measured in pounds, ounces, grams, kilograms or newtons across the width of the web.
Tension Calculation
Mathematically, tension equals torque divided by radius. This means that as a roll diameter increases or decreases, torque must be adjusted to maintain tension at the optimal value, or setpoint. So in a basic sense, by controlling the torque in a uniform manner in relation to the roll, we control tension.
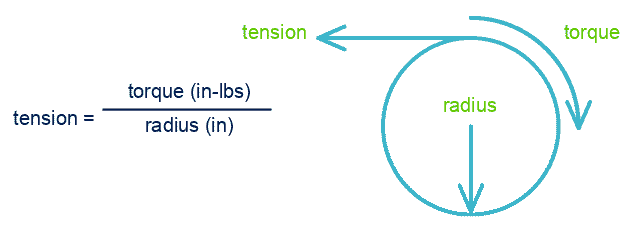
Web Tension Calculation Formula
What is Tension Control?
Tension control is the process of maintaining a predetermined or set amount of stress or strain on a given material between two points to maintain its desired properties (such as form, appearance, etc) and quality. This process often takes place in specific control zones: unwind/payout, process (nip), and rewind/take up, with each having unique tension control requirements.
So tension control is the process of ensuring your material gets from point A to point B in a uniform and consistent manner without any loss to material quality. Under this basic definition, most applications can already get their material processed from point A to B, but perhaps it is very manual or is slower than it could be. In your current application could you double your speed without sacrificing end product quality?
Automating the process, creating a continuous process and increasing productivity are all going to rely heavily on proper tension control to ensure consistent and high-quality results.
How do Tension Control Systems Work?
With a fixed torque in an unwind application, as the roll diameter decreases, the tension applied to the web will increase, and will increase more rapidly as the roll diameter gets closer to core. In rewind applications, it’s just the opposite. As the roll diameter builds, with a fixed torque, tension will decrease as the roll diameter increases.
As a roll diameter increases or decreases, torque must be adjusted to maintain tension at the optimal value, or setpoint. So in a basic sense, by controlling the torque in a uniform manner in relation to the roll, we control tension.
There are three types of tension control:
Manual Tension Control
- Adjustments made via physical or visual inspection
- Result in constant up and down tension changes
Just as it implies manual control is the process of visually or physically determining if tension is correct, and then making manual adjustments to maintain the desired tension level. With manual tension control a web is subject to constant up and down spikes as an operator is always playing with correcting the tension.
Maintaining proper tension gets increasingly difficult as roll diameters decrease and changes happen more frequently. This method is also exposed to the subjectivity of different operators, typically resulting in non-uniform results.
Open Loop Systems
- Adjustments made based on roll diameter
Open loop systems utilize products such as ultrasonic sensors or proximity sensors to measure, or calculate roll diameter. Based on inputs into the controller, the controller uses any detected changes in roll diameter to regulate torque and maintain tension, as opposed to closed loop systems which receive tension feedback directly from the web of material.
Although not as precise as closed loop systems, open loop systems still provide an automated system of consistent tension control that outperform manual control. Open loop systems are generally less expensive than closed loop systems because you are not utilizing additional products, like load cells.
Closed Loop Systems
- Adjustments made based on web feedback
Closed Loop Tension Control refers to a continuous flow of communication from a web tension measurement device, to a torque controller, to a torque device.
Web Tension Measurement devices include load cells or a dancer position feedback sensor, that are constantly relaying tension changes directly from the web of material to the tension controller, which regulates the output of the torque device, which may be a tension brake, clutch, or drive to maintain the desired tension level.
If any changes in tension are detected the controller can instantly alter the torque device to maintain set tension. This ensures that throughout your entire process your tension is consistent, uniform and precise. And all of this happens automatically. We like to use the term “set it and forget it” to describe how a high quality tension control system should operate.
The Benefits of Automated Web Tension Control
Lack of tension control can result in:
- Wrinkles
- Web breaks
- Poor process results
- Interweaving (slitting)
- Poor print registration (printing)
- Inconsistent coating thickness (coating)
- Length variations (sheeting)
- Material curl during laminating processes
- Roll defects (telescoping, starring, etc.)
In both closed loop and open loop, tension is managed by the torque applied to the center of the roll from a brake, clutch, or drive. Tension Controllers automatically regulate this torque, making any necessary correction or adjustments, throughout the process, allowing for continuous production.
Operators simply input the parameters of the production run (such as speed, tension, etc), press start/run and allow the controller to automatically manage production.
As mentioned, one of the key elements to improved productivity and profitability can be traced to the lack of effective tension control. Often we find that due to their manufacturing process or poor tension control, manufacturers are not able to run their material rolls all the way down to the core affecting both productivity and profitability.
This more or less is leaving money on the core, only to end up as scrap. Other sources of scrap and lost productivity come from web breaks, and inconsistent end product. Quality tension control helps to eliminate these scrap producers by creating a uniform and consistent process.
The benefits of a high-quality tension control system include:
- Automated, consistent and continuous production
- Reduced scrap
- Increased end product quality
- Increased productivity
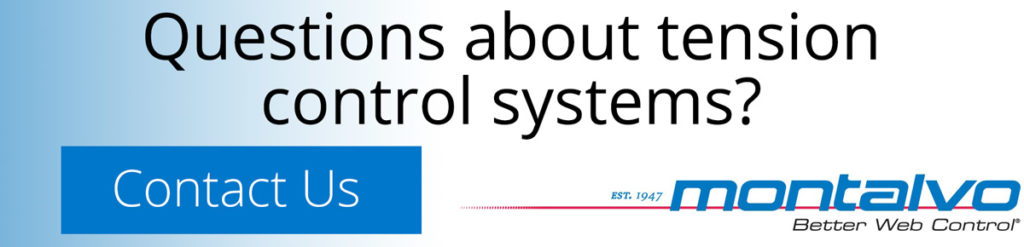